In this project, Svekon has had a close and long-term collaboration with both the product owner Northcone who developed the new pole as well as the machine manufacturer Ortic who developed the production. The result is a durable and crash-proof post that is manufactured in an advanced and fully automated production.
“Svekon has been involved from the beginning and is now accompanying us on the journey to further develop the product. Being able to continue to exchange ideas and work with Svekon is valuable to us. They know what it is about and it makes the work smooth and efficient.”
Anders Blomqvist, Product Manager, Northcone
New innovative design
While the traditional lamp post has pipes as its basic component, Northcone has developed a completely new standard where thin sheet of high-strength steel is roll-formed in 3D into a conically shaped post.
During a long process, Svekon has been involved in the development of the new design and is now working closely with Northcone to further develop and adapt the pole according to the market’s various requirements and wishes.
A crash-proof and durable post
The benefits of the new post are several. Firstly, the post is crash-proof and can slow a car traveling at 100 km/h down to 30 km/h in the event of a collision, which contributes to a safer environment for those traveling in traffic. There are also several environmental aspects. Northcone’s new lamp posts are made of 2 millimeters of high-strength steel, which significantly reduces the material consumption for a post. Since the end product is lighter than a traditional pole, the carbon footprint is also reduced throughout the logistics and handling chain until the pole is fixed in the ground. Last but not least, the pole has a Magnelis coating, which increases its lifespan by providing powerful protection against long-term wear and tear, while the surface coating emits minimal zinc.
“Having a long and successful cooperation with Svekon makes our work easier. They know our needs well, which I think is important.”
Johan Eriksson, CEO, Ortic
Advanced and automated production
In order to produce the post in series in an efficient way, Svekon has helped the machine supplier Ortic to develop an advanced production. The result was a machine that both roll-forms the 2 millimeter thin sheet of high-strength steel through so-called 3D roll forming and then in the same process welds it together into a conically shaped post. A completely finished product then emerges from the machine.
Svekon has delivered solutions for several parts of the machine when it comes to roll forming, but also the welding box that mechanically holds the profile during laser welding. A real challenge because the sheet metal is very thin and the shape of the post is conical.
“The welding box itself was probably the biggest challenge because it had to be very flexible. I am very proud of the end result as a whole and that the machine delivers a high quality end product with no variations.”
Bengt Arén, designer at Svekon
Listen to Anders Blomqvist, product manager at Northcone, talk about the product and the collaboration with Svekon.
Hear Johan Eriksson, CEO of Ortic and Bengt Arén, engineer at Svekon talk about the development of the production.

Johan Eriksson, CEO of Ortic and Bengt Arén, engineer at Svekon in front of a number of finished poles at Northcone’s production facility in Borlänge.
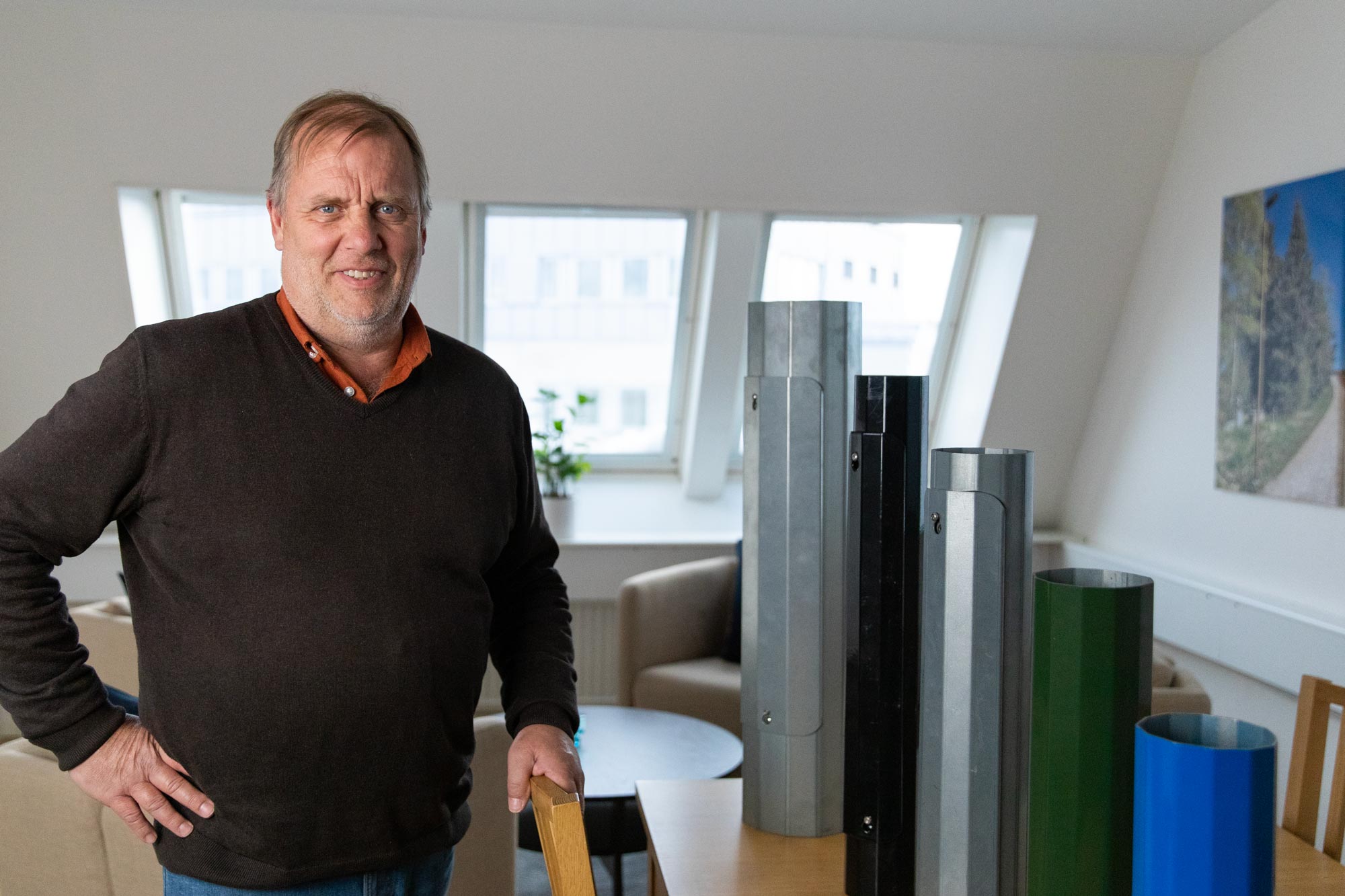
Anders Blomqvist, product manager at Northcone, with parts from different models of the new lamp post.